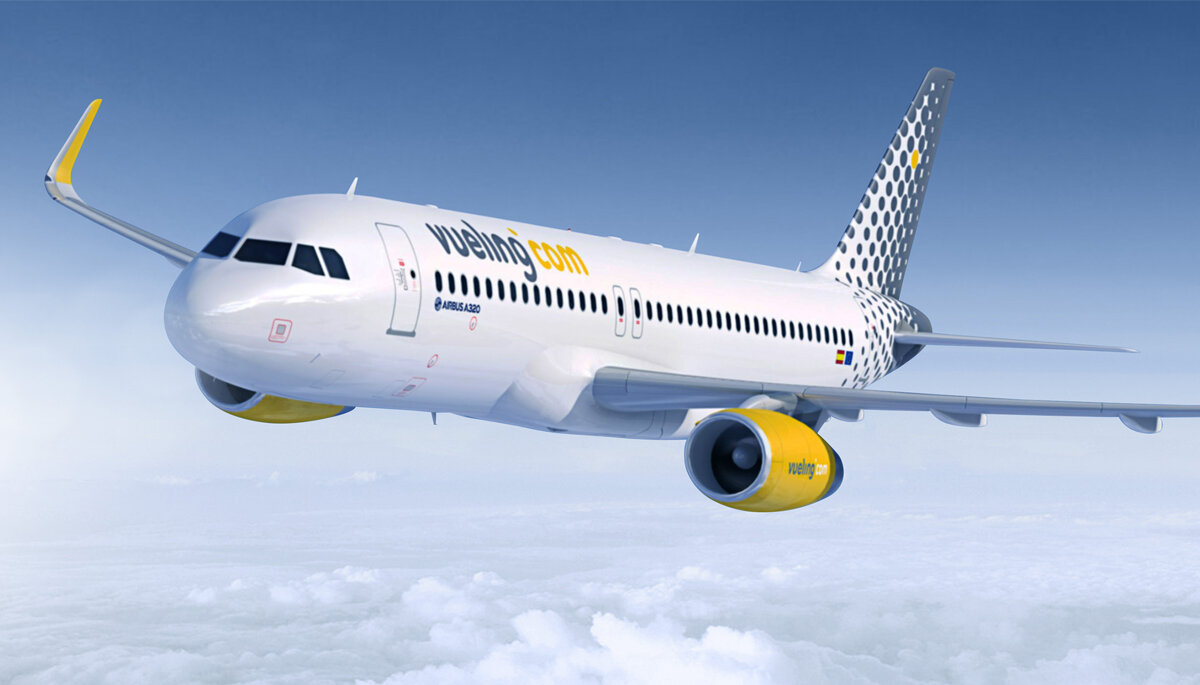
Robotic Process Automation at Vueling
Situation
Vueling was facing a challenge with the printing of work packages from the AMOS frontend that needed to be delivered to the MRO at the end of the day. Every single item in the maintenance forecast is one execution of the process and thus the daily creation of work packages weighed heavily on the daily workload in what was a quite complex process
In fact, three or four employees were engaged on these tasks, with two to three hours each day spent on printing work packages alone—tthere were about 120 work packages a day to be handled. The task is necessary for daily operation but is repetitive, monotonous, and time-consuming. Additionally, the department did not have the resources to always fully cover the workload, thus increasing pressure on the engineers. It meant that the task had to be planned up to seven days ahead, and, more importantly for the business, it meant that those employees involved with this task were skipping non-mandatory forecast items in order to free up the time they needed for printing work packages. That, of course, was bad for the business.
Solution
In order to address the issue that was facing Vueling, EXSYN recommended and Vueling agreed to a solution that introduced Robotic Process Automation (RPA) to take over routine elements in their processes, such as printing work packages. It was also intended to introduce greater consistency and accuracy and reduce mistakes or omissions caused by human error.
In general, RPA is a technology that allows the user to create a software ‘robot’. This robot mimics the actions a human employee would take and does so in the same user interface of the system. Think of data entry into an ERP system, the archiving of files, or downloading data. These automated actions can even lead to a full end-to-end business process. Robots are trained for their tasks with the same instructions that are used for their human counterparts, and every robot also has its own workstation. Instead of a physical station, it is a virtual one. In these virtual environments, they ‘read’ the screen electronically.
One of the biggest strengths of RPA is its low requirement for change in an organisation. Software robots literally mimic the actions that human employees perform and do so on the front-end that human employees use. Organisations can adapt to RPA without having to change their IT infrastructure too much. Additionally, RPA saves organisations from engaging in the risky and time-consuming endeavour of redesigning existing systems or even developing new ones.
By implementing RPA, the business hires a digital workforce. The robot workforce can take care of mundane and repetitive tasks or assist employees in their day-to-day work. Implementing them, organisations can achieve cost reductions of up to 40%, realise improvements in service provision, achieve ROI (return on investment) within one year, and enjoy other benefits.
There are two main automation types: attended automation and unattended automation. Attended automation is automation that is initiated by the human employee and visually runs on the desktop. Unattended automation, on the other hand, is automation that is triggered by an electronic input and executed in a virtual environment.
The Project in Numbers
Tails
Aircraft Types
Source Systems
GB Processed
About Vueling
In July 2004 Vueling commenced with two Airbus A320’s and 4 routes. Now, a little later than 11 years, Vueling operates on 366 routes with a fleet of 100 aircraft and 3,000 flight personnel. Vueling is a low cost airline with its home base at EL Prat airport in Barcelona. Paris Charles de Gaulle, Madrid Barajas, Sevilla, Brussels Airport and Amsterdam Airport Schiphol are also used as hubs. The airline performs direct flights from Barcelona to 155 destinations in Europe, Africa and the Middle East and carries over 16 million passengers every year. Vueling operates on 366 routes with a fleet of 100 aircraft and 3,000 flight personnel. Vueling fleet consists of 100 in a mix of A319s, A320s, and A321s. www.vueling.com